So, some backstory: I used to make whistles. I made them out of exotic hardwoods and also Corian (that stuff countertops are made out of). Link is to a 12 year old thread where I was first advertising the Corian whistles.
http://forums.chiffandfipple.com/viewtopic.php?t=46741
To make whistles by hand, you need:
That said, I don't wanna spend $6000. Nor do I wanna clear out my garage and fill it full of wood and plastic chips that get everywhere. Nor do I want to spend 4 to 6 hours of labor making a whistle which might (due to unseen defects in the wood grain) catastrophically explode and fly apart on the lathe. Thus, my theory: 3d print the things.
I took my $1000 O'Riordan whistle and my micrometer and made a bunch of design diagrams.
Got on Fiverr and started looking for someone to turn those into a shape file for 3d printing. Last night, a guy offered to do it for $5.00. Most of the quotes I got were between $50 (for developing countries) and $360 (a mechanical engineer from Germany). Thought "what the hell? It's only $5.00. If it doesn't work out, I can still get one of the other guys to do it."
Woke up this morning with this in my mailbox:
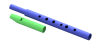
Threw the .STL files in a viewer, and they look good, with good dimensions, so, I sent them off to Shapeways to have a prototype made, which should arrive first of July.
Total cost so far: $55. Kinda excited
http://forums.chiffandfipple.com/viewtopic.php?t=46741
To make whistles by hand, you need:
- A long bed wood lathe. Used to rough a wood blank into a cylinder, and to hold the drill for drilling the long bore. I got a crap one from harbor freight for about $400.
- a self-centering implement to drill the bore, which has minimum wander. Reamers and gun drills are the implements of choice. I used a gun drill, and it cost me $300 for the drill bit.
- An air compressor. Gun drills are hollow, and you blow something down them to keep them cool and clear chips. When drilling metal (for guns) a coolant fluid is used. For wood, you use air. This set me back about $59. But it barely did the job. If I were to do it again, I'd get a $200 model.
- A machine lathe, because precision counts if you want your musical instruments to be in tune. I got a mini lathe from china for about $800.
- lathe tool bits and other parts such as shims. (this stuff ain't cheap yo). I probably spent $100 here.
- A drill press and associated parts (jigs for holding a cylinder, drill bits, etc). Probably spent $250 here.
- Various parts and bits: micrometers, calipers, breathing masks, goggles, etc.
- A table saw for cutting wood and corian down to 12x1x1 size. Spent about $600.
That said, I don't wanna spend $6000. Nor do I wanna clear out my garage and fill it full of wood and plastic chips that get everywhere. Nor do I want to spend 4 to 6 hours of labor making a whistle which might (due to unseen defects in the wood grain) catastrophically explode and fly apart on the lathe. Thus, my theory: 3d print the things.
I took my $1000 O'Riordan whistle and my micrometer and made a bunch of design diagrams.
Got on Fiverr and started looking for someone to turn those into a shape file for 3d printing. Last night, a guy offered to do it for $5.00. Most of the quotes I got were between $50 (for developing countries) and $360 (a mechanical engineer from Germany). Thought "what the hell? It's only $5.00. If it doesn't work out, I can still get one of the other guys to do it."
Woke up this morning with this in my mailbox:
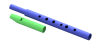
Threw the .STL files in a viewer, and they look good, with good dimensions, so, I sent them off to Shapeways to have a prototype made, which should arrive first of July.
Total cost so far: $55. Kinda excited

Last edited: